The need for a Global Vision
Frederic Dufour / Jun 05 , 2018As previously concluded in Why current management techniques need to be put into question and Misconceptions of Lean Management, management methods are constantly evolving, and traditional ways are losing their relevance. Companies can no longer rely on strict, top down, hierarchical management. Instead they must work to develop strong multi-level relations between directors and employees. High levels of involvement prompt high levels of productivity. Furthermore, companies must adopt a global vision of their various departments as attempting to improve specific operations at a time is time consuming and less than optimal.
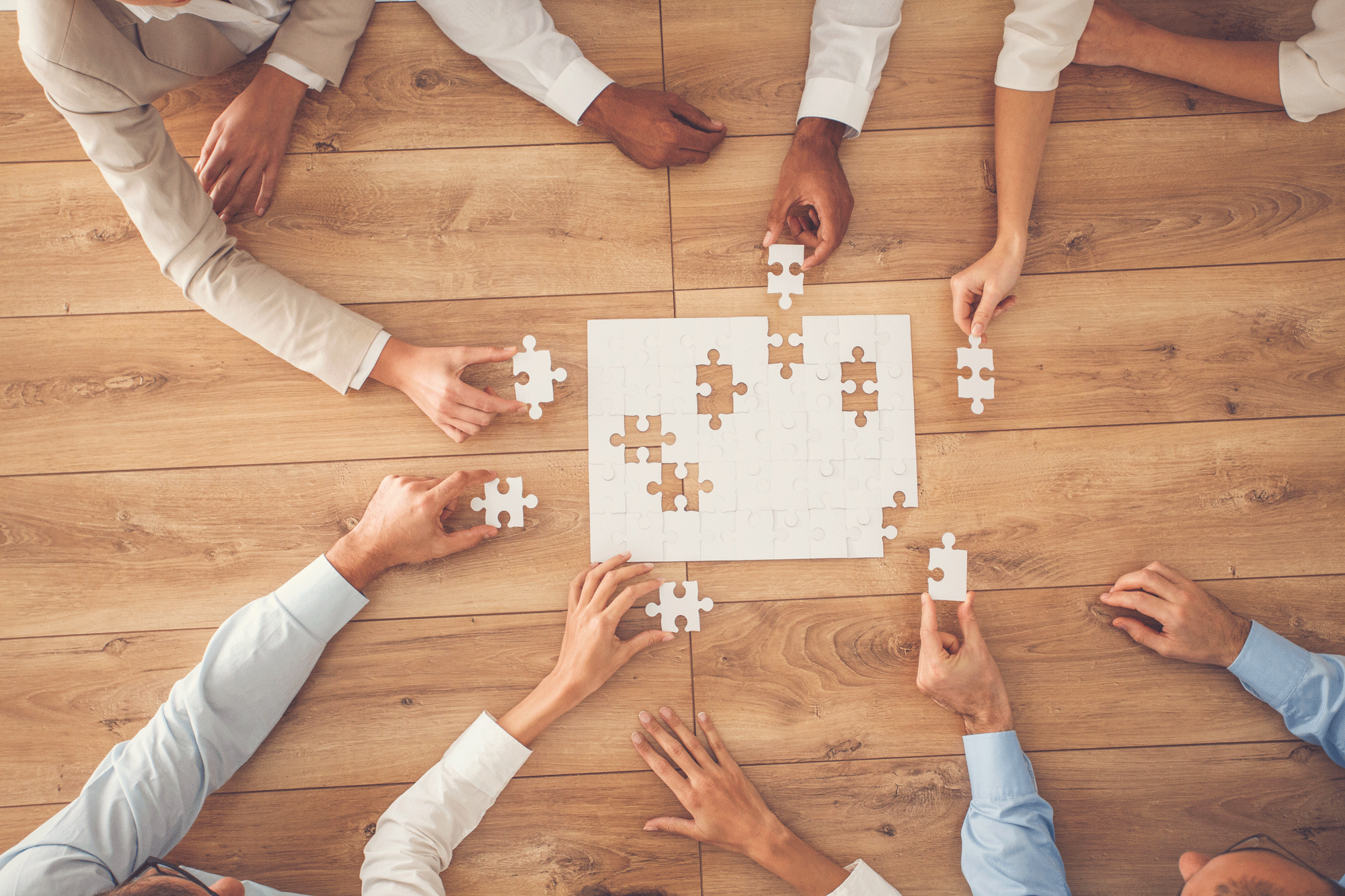
Too often, implementations are too specific as techniques focus on one aspect of management at a time. Resources are mainly considered in terms of their individual costs instead of basing them on their contribution to global performance. The well-being of employees is sacrificed to benefit the company through immediate return on investment, and the value of knowledge and informal exchanges between employees is taken for granted. Finally, employees are often put into question as the quest to understand why decisions were made and mistakes occurred are overlooked. This is because it is easier to point a finger at “who”, than trying to understand “why”.
As Deming demonstrated, these approaches can only lead to effects contrary to those desired. Employees must be acknowledged and well treated for companies to thrive in the modern era. Undesired effects arise from the flawed implementation of these techniques. Tensions develop between departments or hierarchical levels, slurring the effective communication that generates high levels of productivity. Companies lose out as levels of knowledge and know-how decrease following a loss of unhappy and unmotivated employees, and naturally, the quality of the service and client satisfaction drop accordingly. Costs of coordination are high, and companies lose out on commercial and operational opportunities. These negative spirals continue to deteriorate like a vicious cycle as constant changes demand continuous adaptation.
By confusing the causes and consequences, these techniques wrongly appear to be costly to the company, restrictive to its users and penalizing to its employees.
In order to achieve positive effects on the company’s profitability, the Lean management techniques implemented must become part of the company’s philosophy for long-term investment. In the long run, these techniques engender valuable effects across all levels of the company. This is thanks to the Lean processes that make better use of the resources at hand. Happier resources contribute to an increased overall performance throughout the company.
The urgency of today’s competitive environment must, however, push us to find innovative solutions that guarantee effectiveness, both in terms of the company’s profitability and employee well-being. These measures should neither be too costly for the company, too burdensome for the employees, nor too complex to implement.
The adoption of Lean Management is an investment conducive to achieving exceptional results in the long term. To improve short term performance, an array of other techniques can be used to complement the Lean Manufacturing Techniques adopted. This is where ELP and PlanningForce can help you.
Print
Download
More ARTICLES
You may also like
The relaunch of the production tool following COVID 19
This article discusses the immediate and future consequences of the Coronavirus crisis. More specifically, we address the economic dimension of the crisis
Where do I gain with PlanningForce – part 1
This article presents the benefits of using PlanningForce related to optimizing the use of resources, the introduction of new projects and sales cycles.
The seven steps to choose project portfolios that generate high returns
This article describes the process to be followed in PlanningForce to identify how to combine project and resource portfolios in the most cost-effective way.