Current Management must be put into question – part 1
Frederic Dufour / Feb 12 , 2018Management traditionally revolves around two main processes. The first is the Horizontal process that steers the planning processes according to orders, and the second is the Vertical process. In the Vertical process, the department steers the planning process.
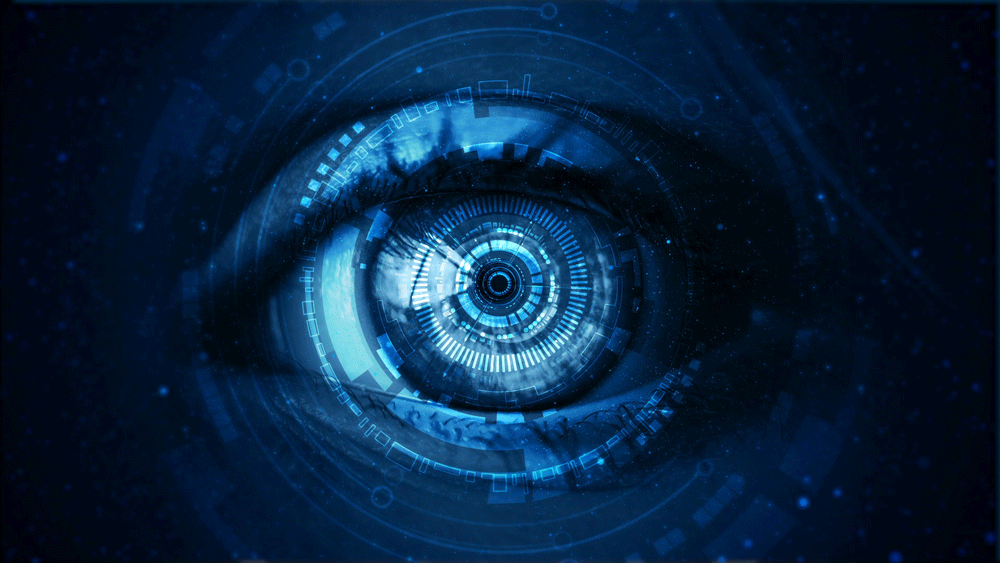
The Horizontal Process
This process is most commonly encountered in firms that have developed expertise in the management of complex requisition orders. It emphasizes the role of the project leader who has to take care of orders from A to Z. This planning mode requires a detailed description of order phases and operations, as well as a budget analysis determined on the basis of standard time delays and costs. Furthermore, firms that give priority to this kind of process put project leaders in positions of great responsibility as they are the ones to ensure that orders are filled appropriately, in terms of quality, cost and deadlines.
But this form of management bears disadvantages too. This model pays little attention to resources and their effective utilization; this can result in large disparities between what is forecast and the reality. Giving priority to projects and operations to be carried out can also hinge more on the influence of the project leader within the firm than on rational decision making. Finally, production and logistics constraints are rarely taken into consideration.
This planning model therefore has a tendency to occasion an increased number of project leaders, a systematic recourse to subcontracting and overtime and non-optimal management of supply and logistics. These factors in addition to its short-sightedness with respect to opportunities which the sales force could put to good use if they had greater visibility of how resources are going to be used and of the resource capacities which the firm could mobilize, shows that the planning model could be improved.
The Vertical Process
This process is often encountered in businesses that pride themselves with strong business expertise. The departments in which the business expertise expresses itself are able to organize their activities with a high degree of autonomy. This is beneficial as the desire for quality affects how work is organised, and the operations carried out. Because of the autonomy, the department has the flexibility to optimize its scheduling by combining tasks, and possibly even part of the logistics and supply.
On the other hand, this model creates tension between departments as they tend to blame one another if mistakes surface. This planning model can also problematically create bottlenecks that yield losses both upstream and downstream. Red tape and delays also occur as the model complicates consolidating data across the business as a whole.
Ergo, the planning model causes an escalation in the number of operational resources, such as human and material resources. Furthermore, it evokes a form of protectionism amongst department leaders with respect to their associates, processes and technologies used. This makes it very difficult to question its functioning.
Communication can also deteriorate as walls go up between departments. This is problematic as the finalization of new products and solutions that require close cooperation between different departments are more onerous and take longer than they would in a “horizontal” process.
Finally, this model is not customer-oriented. This is because it implicitly gives priority to fulfilling operations rather than overall fulfillment, which is to say, of the requisition order.
This is why PlanningForce has since come up with a planning model that seeks to resolve the issues mentioned above. This planning model is instead guided by the quest for a global optimum. This means that PlanningForce’s planning model works to improve companies as a whole. The following article will discuss the advantages of the PlanningForce process over the horizontal and vertical traditional processes.
Print
Download
More ARTICLES
You may also like
Why management techniques must (always) be questioned
Deming and Öno revolutionized the way of producing. While paying tribute to them, this article shows that each era brings new challenges in terms of management.
What is our Vision? What is our Mission?
In an increasingly complex world where major challenges must be met, it is more important than ever to base its development strategy on a clear vision and strong values.
Tactical Steering assisted by PlanningForce
This article details how a company's value chain can be orchestrated through the execution of a planning cycle carried out at the tactical level.