L4 – Execution Steering
PlanningForce’s execution steering gives management the means to track progress in real time for truly effective agile management.
scroll down
|
L4 – Execution Steering
PlanningForce’s executional steering gives managers the means to track progress in real time for truly effective agile management.
Solutions
Execution steering
Execution steering is responsible for monitoring the progress of activities in real-time. It records events and incidents as they occur, enabling line managers and team leaders to quickly identify stoppages or deviations and determine how to adapt sequences of operations accordingly.
“I cannot imagine working without PlanningForce! Our schedule is displayed on a large screen in the design office and in our workshops.”
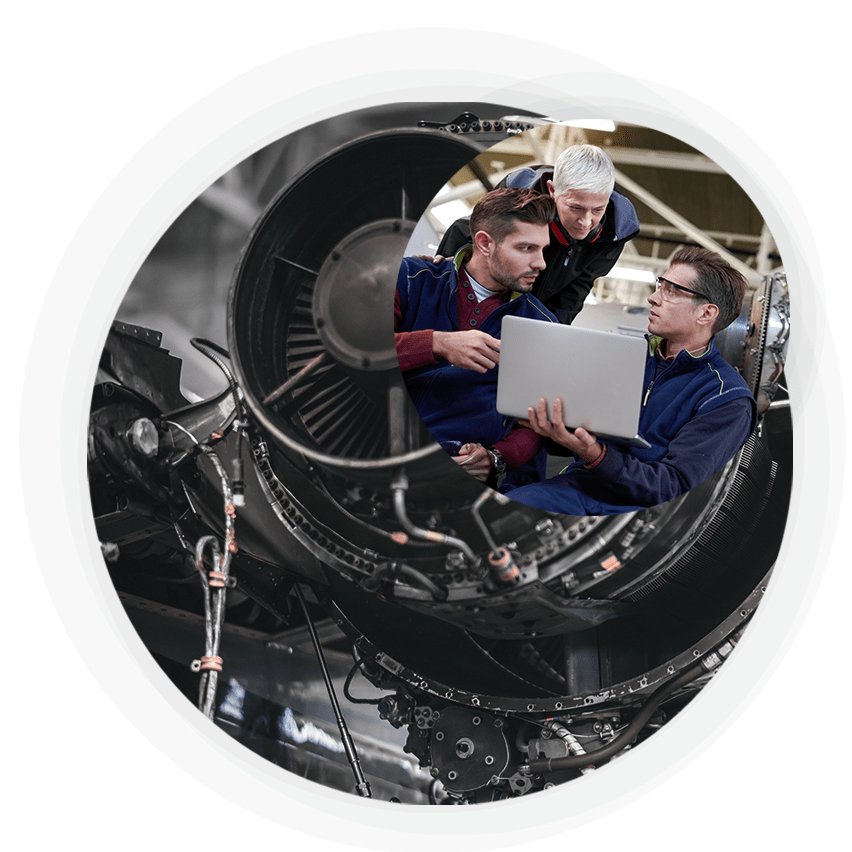
Give your operational teams modern, customized tools on their workstations to enable them to record real-time progress and events as they occur.
At PlanningForce, we know how important it is to record progress at the workstation level in order to finalize the PDCA cycle and capture relevant information to improve future planning and execution of activities. This is why we have specifically designed tools that will facilitate this data entry, whether it is done automatically through equipment or entered manually by operators.
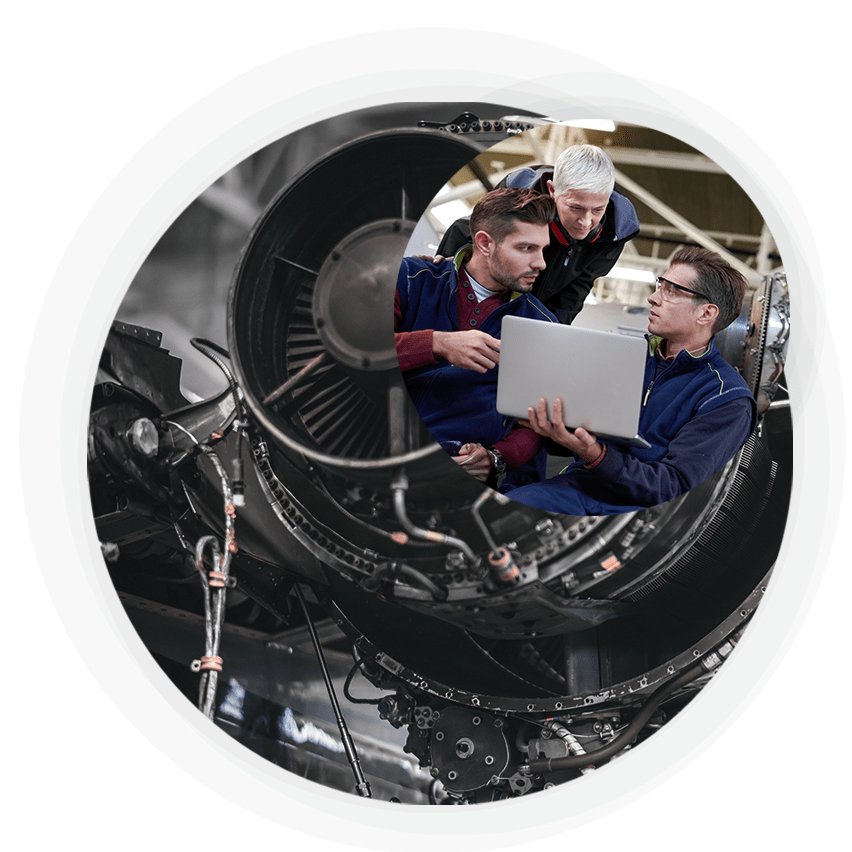
Give your operational teams modern, customized tools on their workstations to enable them to record real-time progress and events as they occur.
At PlanningForce, we know how important it is to record progress at the workstation level in order to finalize the PDCA cycle and capture relevant information to improve future planning and execution of activities. This is why we have specifically designed tools that will facilitate this data entry, whether it is done automatically through equipment or entered manually by operators.
With PlanningForce’s execution steering tools,
there is no longer any excuse for not recording progress at the workstation
Progress recorded from the equipment
When recordings are carried out by a connected machine, the recordings of the quantities produced are made according to the case and the type of machine. This is done either via an exchange of inputs/outputs by network or via an exchange of inputs/outputs by hardware.
These exchanges will collect the quantities realized by distinguishing the good quantities and the scraps in real time. They will provide information on the status of the machines (running, stopped, broken down, etc.) and will automatically launch maintenance operations if necessary. They will also record set-up and running times.
With this information, OEE reports can be made by machine, workshop or production types. Many other reports can be automatically generated, such as the Pareto of machine interruptions and synthetic views on the assignment of a workshop’s machine park.
Progress recorded manually
Even in an industry 4.0, many task progress records continue to be recorded manually by operators. Even in the case of a recording carried out automatically by the machine itself, the operator remains the main actor in charge of validating and correcting data before it is fed back into the various information systems.
PlanningForce has designed easy-to-use solutions because these recordings are vital to the smooth running of your operational processes, but also because your teams are probably too busy with daily tasks to devote much time to learning new complex tools.
The ergonomics and workflows of these tools have been studied with the users so that their adoption is not seen as an additional constraint, but rather, as a concrete aid that will simplify their work and, ultimately, set up modern and efficient management of operational activities.
Desktop or mobile application
As the operator’s companion on his workstation, the tool used to record the task progress will take the form that best suits the workstation and the needs of the job.
The engineer or draftsman of a design office will open a web page that will allow him to select the task to be performed and to point out the time completed and the work remaining.
The industrial operator will have a PC or tablet in order to start an activity, put it on hold or close it, perform the various part counts or make calls to maintenance, quality, the supervisor or the warehouse. This PC or tablet will ideally be connected to a machine or a scanner.
Finally, the operator or supervisor present on the worksite will have access to a mobile version that will allow him to record the progress of operations as well as disruptive events and incidents that will require a re-planning phase.
With PlanningForce’s execution steering tools,
there is no longer any excuse for not recording progress at the workstation
Progress recorded from the equipment
When recordings are carried out by a connected machine, the recordings of the quantities produced are made according to the case and the type of machine. This is done either via an exchange of inputs/outputs by network or via an exchange of inputs/outputs by hardware.
These exchanges will collect the quantities realized by distinguishing the good quantities and the scraps in real time. They will provide information on the status of the machines (running, stopped, broken down, etc.) and will automatically launch maintenance operations if necessary. They will also record set-up and running times.
With this information, OEE reports can be made by machine, workshop or production types. Many other reports can be automatically generated, such as the Pareto of machine interruptions and synthetic views on the assignment of a workshop’s machine park.
Progress recorded manually
Even in an industry 4.0, many task progress records continue to be recorded manually by operators. Even in the case of a recording carried out automatically by the machine itself, the operator remains the main actor in charge of validating and correcting data before it is fed back into the various information systems.
PlanningForce has designed easy-to-use solutions because these recordings are vital to the smooth running of your operational processes, but also because your teams are probably too busy with daily tasks to devote much time to learning new complex tools.
The ergonomics and workflows of these tools have been studied with the users so that their adoption is not seen as an additional constraint, but rather, as a concrete aid that will simplify their work and, ultimately, set up modern and efficient management of operational activities.
Desktop or mobile application
As the operator’s companion on his workstation, the tool used to record the task progress will take the form that best suits the workstation and the needs of the job.
The engineer or draftsman of a design office will open a web page that will allow him to select the task to be performed and to point out the time completed and the work remaining.
The industrial operator will have a PC or tablet in order to start an activity, put it on hold or close it, perform the various part counts or make calls to maintenance, quality, the supervisor or the warehouse. This PC or tablet will ideally be connected to a machine or a scanner.
Finally, the operator or supervisor present on the worksite will have access to a mobile version that will allow him to record the progress of operations as well as disruptive events and incidents that will require a re-planning phase.
BLOG
Related Articles
Factory of the Future, a structuring framework
A Factory of the Future is deemed both a label and a framework. The prestigious award is awarded to the most advanced and best performing Belgian manufacturing industries.
The importance of developing tools that will reconsolidate companies with their initial drive
This article sheds light on the traditional planning methodologies and tools that hinder companies in their efforts to become agile, efficient and attractive.
Reenchanting the Enterprise – part 1
This article addresses one of the main challenges of modern management: how to make the company attractive to its stakeholders in the long term.
More SOLUTIONS
What fits to your needs