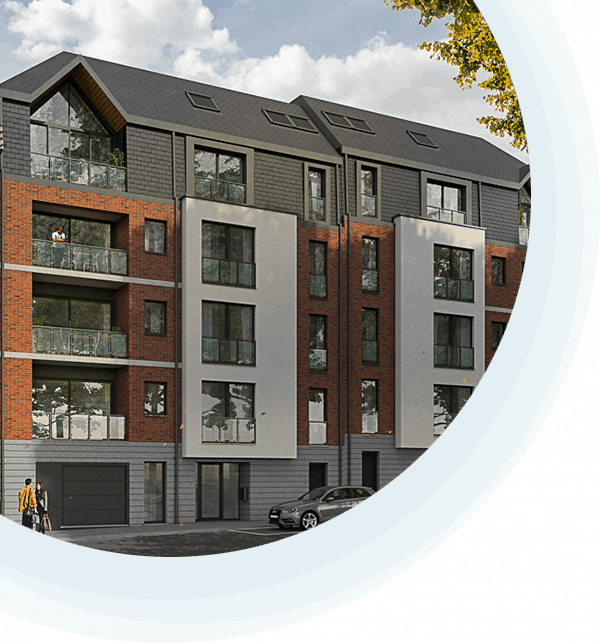
Engineering – Construction
Sotraba
Levels implemented :
L2 – Tactical | L3 – Operational | L4 – Execution
Services used :
Process Consultancy | Technical Consultancy | Custom Development | Training and Support | IT and Hosting
Products used :
APS | TRP | DEP | TEA | CSO | DWH | ARA | API | ART | ADM
Print
Download
They lead in
SOTRABA is a construction company based in Belgium that has been acquired by the Belgian Thomas & Piron Group. SOTRABA has recorded steady growth for more than 5 years now. This has led to an increasing complexity in terms of resource allocation, project monitoring, team coordination, project administration and supply management.
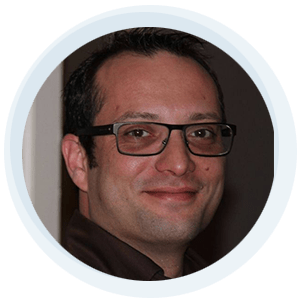
By bringing together all our information channels with PlanningForce : we respect our delivery deadlines, we are sure to order at the right time: not too early so as not to tie up working capital unnecessarily, but not too late either so as not to block the construction site, we anticipate overload, we monitor the time spent by each resource on projects and tasks, we follow up on customer invoicing based on actual progress and we generate accurate cash flow dashboards.

Situation
Similarly, to many companies within this sector of activity, SOTRABA works with its own project engineers, site supervisors and teams of masons. As it grew, the limits of Excel became apparent and the top management of SOTRABA was in need of a solution that could help them to, not only better manage the day-to-day business, but also structure the company in a new way. These changes would be favourable as the new organization could better support future growth. The company seeks to become the most efficient and profitable company of the Thomas & Piron Group, as this would shed a positive light on the group and reference SOTRABA’s good management practices.
Task
SOTRABA wanted to benefit from a completely integrated solution. Integrated meaning: integrated with their “ERP” system (technical integration), integrated between the different departments (horizontal integration), integrated with the execution (vertical integration) and finally, integrated with the subcontractors (external integration).
Action
The solution built around PlanningForce involves most modules apart from strategic planning. All projects are transferred from the ERP system to PlanningForce, where a “central planner” steers the introduction of this new project.
Phase 1
A preliminary study is conducted to evaluate the feasibility and the cost of this new project at the Study Bureau. If the project is accepted, its status changes and it will then be managed by a Project Manager who is in charge of the whole life cycle of the project. The project is planned by the Project Manager, but the schedule is decided by the Central Planner who controls the bigger picture (i.e. the usage of the resources at the study bureau and the teams of masons).
Phase 2
A site supervisor is then assigned to the daily monitoring of the execution. The site supervisor is expected to assess the progress of the task on a daily basis. He must record the progress and any possible problems encountered.
Phase 3
All stakeholders, including subcontractors, are informed about these occurrences, whether they involve progress or problems leading to delays. Every week, the project manager centralizes the progress, so he can eventually detect any deviations and take appropriate action. The progress is then centralized on a bimonthly basis, where the central planner can write reports and prepare a new plan on the basis of new project introduction and the progression of projects in progress.